- Welcome to the MSI USA website. MSI designs and creates Mainboard, AIO, Graphics card, Notebook, Netbook, Tablet PC, Consumer electronics, Communication, Barebone.
- Displays / Desktops Motherboards / Components Networking / IoT / Servers. ASUS Download Center Download the latest drivers, software, firmware and user manuals. Enter a model name or select a product to find drivers, manuals, warranty information and more.
Wistron plays a key role in understanding and controlling every step of the supply chain. With a highly integrated project management process, advanced information systems and tight professional control over parts suppliers, Wistron helps to ensure optimum utilization and efficiency of the supply chain.
Home / Products & Services / Design/Manufacture/Services / Manufacturing
Wistron's tremendous and long manufacturing history will provide a full range of industry-leading manufacturing services. From the circuit board assembly, barebones assembly, systems integration - including post-production orders and customized production to all relevant quality assurance testing. Wistron, a world-renowned manufacturer, has produced information products for other brand names. Its manufacturing process is often complex because it involves a number of manufacturers from different countries to work together to complete.
Rich experience in manufacturing means Wistron can carefully combine product and manufacturing process development phase, thus creating a more efficient new product introduction process. Because of Wistron intense understanding of the many concerns of customers, we have developed flexible manufacturing processes and IT infrastructure, to manage and control needs of customers more efficiently.
All processes and information can be monitored and managed real-time by the site factory control systems (SFCS). Through order tracking system (OTS), customers can even track status of parts. With the link of clients and Wistron, it optimizes the efficiency of the process flow of information. They are sufficient to enhance the overall customer product introduction plans and prepare products for after sales service.
Assembly services
Wistron provides complete motherboard and system assembly services to meet the increasing demands of our customers. Through our production scheduler, our customers can take advantage of our flexible manufacturing services and comprehensive information system by using different models or modes of operation for different products—including standard full-system assembly, built-to-order or post-order production orders (BTOs), and configure-to-order or customized production services (CTOs). For planned BTO and CTO products, the planned turnover is reached by a systematic process. Wistron's integrated system also provides single assembly and single shipment processes.
Manufacturing Capability |
|
Quality control
Wistron quality policy of zero defects and competitive products and services delivered to customers on time.
Quality Management System | To be a leading global information and communications technology industry service provider (TSP), Wistron's quality management system relies on the consistency of ISO speaking, writing, and execution, combined with continuous improvement. Our PDCA management cycle is an integral part of our daily operations, ensuring that high-quality policies can be implemented. The goal of our quality management system is to be a leading global information and communications TSP. Wistron emphasis on product quality management system combines assurance for both product design quality and manufacturing process quality control. The assurance of design is more important than failure prevention. In the initial stages of design the customer requirements for the product are transitioned into design requirements and design parameters and parts specifications. By integrating circuit board layout verification, product reliability verification, the operating system validation, audio visual verification, and electromagnetic radiation certification, they will support the development of a series of internal and external certifications designed to meet the customer demand for the products. In terms of the quality control process, through risk analysis and management, combined with statistical process control and acceptance sampling plan, we will be able to reduce product variation in the most economical way to ensure the quality of shipments. After the product shipment, with production yields and market feedback information, a EWG meeting with design and production departments will continue product quality checks to implement the spirit of the quality management system. |
Process Quality Inspection | Subsequent quality inspections at various stages of the manufacturing process enable us to execute our production plan in accordance with the preset schedule and to meet customers' quality expectations. The starting point of our testing process is a rigorous inspection that occurs immediately after parts are received, in order to ensure the quality of the supplier. The final check point is an inspection of assembled and packaged samples. Wistron also has proprietary test stations to implement a set of industry-standard tests. The results often exceed the expectations of customers. Wistron testing process is evolved from a wealth of information and communications products manufacturing experience. Through testing at the various stages of the process we will be able to confirm precise conformation to the original product design so that any problems in the production process can be correctly quickly. After combining with advanced tools, equipment and expertise we will be able to detect any defective boards / parts. At the same time we will provide in-depth analysis of specific issues in the production of information and communications products. After detecting the root causes of problems, QA engineers will assist to prevent similar problems from happening again, and thus raise the overall manufacturing standards. |
Quality Management |
|
Testing Applications |
|
Supply chain management
Wistron plays a key role in understanding and controlling every step of the supply chain. With a highly integrated project management process, advanced information systems and tight professional control over parts suppliers, Wistron helps to ensure optimum utilization and efficiency of the supply chain. Therefore, customers can be confident, from product development, production, to after-sales service, which they are under good management and control.
Even the use of integrated parts, the high number of parts used in a single product is very surprising. With the ever-shortening product cycles, more products reach the market faster than ever. In addition, the fact that different manufacturing centers are to serve customers and manage global suppliers, adds to the complexity of management. Our customers increasingly rely on Wistron to work closely to develop the best parts procurement plan and complete the delivery of products. It also includes the use of parts supply service required at present or in the future.
Wistron's tremendous and long manufacturing history will provide a full range of industry-leading manufacturing services. From the circuit board assembly, barebones assembly, systems integration - including post-production orders and customized production to all relevant quality assurance testing. Wistron, a world-renowned manufacturer, has produced information products for other brand names. Its manufacturing process is often complex because it involves a number of manufacturers from different countries to work together to complete.
Rich experience in manufacturing means Wistron can carefully combine product and manufacturing process development phase, thus creating a more efficient new product introduction process. Because of Wistron intense understanding of the many concerns of customers, we have developed flexible manufacturing processes and IT infrastructure, to manage and control needs of customers more efficiently.
All processes and information can be monitored and managed real-time by the site factory control systems (SFCS). Through order tracking system (OTS), customers can even track status of parts. With the link of clients and Wistron, it optimizes the efficiency of the process flow of information. They are sufficient to enhance the overall customer product introduction plans and prepare products for after sales service.
Assembly services
Wistron provides complete motherboard and system assembly services to meet the increasing demands of our customers. Through our production scheduler, our customers can take advantage of our flexible manufacturing services and comprehensive information system by using different models or modes of operation for different products—including standard full-system assembly, built-to-order or post-order production orders (BTOs), and configure-to-order or customized production services (CTOs). For planned BTO and CTO products, the planned turnover is reached by a systematic process. Wistron's integrated system also provides single assembly and single shipment processes.
Manufacturing Capability
|
Quality control
Wistron quality policy of zero defects and competitive products and services delivered to customers on time.
Quality Management System To be a leading global information and communications technology industry service provider (TSP), Wistron's quality management system relies on the consistency of ISO speaking, writing, and execution, combined with continuous improvement. Our PDCA management cycle is an integral part of our daily operations, ensuring that high-quality policies can be implemented. The goal of our quality management system is to be a leading global information and communications TSP. Wistron emphasis on product quality management system combines assurance for both product design quality and manufacturing process quality control. The assurance of design is more important than failure prevention. In the initial stages of design the customer requirements for the product are transitioned into design requirements and design parameters and parts specifications. By integrating circuit board layout verification, product reliability verification, the operating system validation, audio visual verification, and electromagnetic radiation certification, they will support the development of a series of internal and external certifications designed to meet the customer demand for the products. In terms of the quality control process, through risk analysis and management, combined with statistical process control and acceptance sampling plan, we will be able to reduce product variation in the most economical way to ensure the quality of shipments. After the product shipment, with production yields and market feedback information, a EWG meeting with design and production departments will continue product quality checks to implement the spirit of the quality management system. |
Process Quality Inspection Subsequent quality inspections at various stages of the manufacturing process enable us to execute our production plan in accordance with the preset schedule and to meet customers' quality expectations. The starting point of our testing process is a rigorous inspection that occurs immediately after parts are received, in order to ensure the quality of the supplier. The final check point is an inspection of assembled and packaged samples. Wistron also has proprietary test stations to implement a set of industry-standard tests. The results often exceed the expectations of customers. Wistron testing process is evolved from a wealth of information and communications products manufacturing experience. Through testing at the various stages of the process we will be able to confirm precise conformation to the original product design so that any problems in the production process can be correctly quickly. After combining with advanced tools, equipment and expertise we will be able to detect any defective boards / parts. At the same time we will provide in-depth analysis of specific issues in the production of information and communications products. After detecting the root causes of problems, QA engineers will assist to prevent similar problems from happening again, and thus raise the overall manufacturing standards. |
Quality Management
|
Testing Applications
|
Supply chain management
Wistron plays a key role in understanding and controlling every step of the supply chain. With a highly integrated project management process, advanced information systems and tight professional control over parts suppliers, Wistron helps to ensure optimum utilization and efficiency of the supply chain. Therefore, customers can be confident, from product development, production, to after-sales service, which they are under good management and control.
Even the use of integrated parts, the high number of parts used in a single product is very surprising. With the ever-shortening product cycles, more products reach the market faster than ever. In addition, the fact that different manufacturing centers are to serve customers and manage global suppliers, adds to the complexity of management. Our customers increasingly rely on Wistron to work closely to develop the best parts procurement plan and complete the delivery of products. It also includes the use of parts supply service required at present or in the future.
Home / ESG / Society / Product Quality and Safety / A Focus on Product Liability and Product Quality Management
Wistron incorporates green product management practices in accordance with the ISO9001 Quality Management System and has obtained the IECQ QC 080000 management system certification. The raw materials of Wistron parts must abide by international or regional environmental regulations (e.g., RoHS, REACH, etc.), local government environmental policies (e.g, China RoHS, Japan RoHS, California Proposition 65, etc.), voluntary environmental regulations (China Compulsory Certificate (CCC), Electronic Product Environmental Assessment Tool (EPEAT), etc.), and special environmental regulations (e.g., conflict minerals, etc.) All of Wistron's product lines comply with EU RoHS regulations. As requested by our customers, we also avoid using specific hazardous substances that are harmful to the human body or the environment (e.g., halogen-free perfluorooctanesulfonic acid and polycyclic aromatic hydrocarbons).
Wistron develops products in compliance with customer requirements, local energy laws and regulations, and safety regulation labels from different regions, such as Energy Star. These labels are then affixed on product exteriors, packaging, or instruction manuals. Different product lines have passed energy consumption regulations of different regions, such as the European Union's ErP, South Korea's E-Standby, and China Energy Label, as requested by our customers. In 2019, more than 97.22% of mass production products such as laptops, desktop computers, and LCD monitors obtained the ENERGY STAR certification pursuant to the strategic requirements of energy demand.
Wistron's products protect consumer safety and health
Wistron Safety Laboratory has obtained the UL Client Test Data Program certification. This lab regularly reviews the laboratory quality plan through certification units to meet the ISO 17025 standard and periodically confirms the test data to maintain its testing capability and quality to protect consumers and their property. All Wistron mass production products are 100% compliant with IEC 60950-1 safety standards under the information technology equipment (ITE) category, and 100% compliant with IEC 60065 safety standards under the Audiovisual (AV) product category. With the advancement of technology, different types of products are being developed, making product classification extremely difficult. Wistron actively integrates the new standard IEC 62368-1 into its product design, becoming the first system manufacturer to pass the new standard and meet the test qualification in Asia. To prevent potential risks, Wistron shifts from passively abiding by safety requirements to actively preventing potential risks so as to ensure that all types of products completely meet safety regulations to further protect consumers' health and safety. Not only do all products become certified before they are sold in the market, product safety is consistently and continuously checked from time to time after mass production.
In 2019, all product lines were completely compliant with customers' requirements and local energy laws, and energy and safety labels, and was not involved in violations of voluntary regulations as well as laws and regulations concerning product information labeling.
A Focus on Product Liability and Product Quality Management
In today's rapidly changing business environment, excellent product quality is a significant determinant of a company's operating status and the foundation of the company's competitiveness. To guarantee high product quality, Wistron utilizes an ISO-based quality management system and implements a quality policy that states: 'To deliver defect-free, competitive products and services to our customers on time.' In accordance with this quality system and policy, Wistron adopts a top-down approach to monitor, measure, analyze, and continuously improve quality-related indicators; strictly implement related control process of “speaking, writing, and doing”; and manage daily operations with the plan-do-check-act (PDCA) practice so as to ensure that our quality goals are specifically implemented.
Product quality verification
Wistron's product designs must pass relevant quality verification tests to ensure that products meets specifications and customers' quality requirements before mass production, including functional verification, compatibility tests, reliability verification, environmental specification requirements, and the DFx (Design For Manufacture/ Assembly/ testing/ Service). Meanwhile, through the establishment of the Lessons Learned database and early participation in the product design and experimental stages of Wistron's factory, the product design capability, ease of production, and quality of produced products are continuously improved.
Supplier Quality Management
Wistron Laptops & Desktops Driver Download
The quality of products produced is positively related to the quality of raw materials. Therefore, before production and use, Wistron will confirm that the raw materials meet the specifications and quality requirements, and will list the quality of raw materials as a key item for rating suppliers. Quality management auditing is also performed on suppliers. Wistron requests suppliers to improve non-conforming items in quality management or auditing by a specific deadline, and concurrently conducts quality control on materials and supply chains in order to ensure that the quality of the products produced adheres to customer requirements and specifications.
By organizing a green supplier conference, Wistron guides suppliers to strengthen their actions and response to the latest requirements of international environmental laws, improve their product quality, collectively build a green supply chain for Wistron, and work hand in hand to strive toward product sustainability and development. The 2019 Wistron Green Supplier Conference was held in Taipei, Zhongshan, Kunshan, and Chongqing, with over 900 participants. During the Green Supplier Conference, Wistron collaborates with technologists to share with suppliers Wistron's CSR practices and regulatory trend, introduce the Wistron supplier questionnaire survey platform (SQP), and teach suppliers practical operations through GPM system completing on the Material Composition Declaration (MCD) and Full Material Disclosure (FMD). In addition, RoHS testing method was used to educate all supplier partners on Wistron's strategic requirements and implementation methods with regards to “green environmental protection” to ultimately improve corporate quality management, promote the sustainable development of electronic industries, and fulfill corporate social responsibility.
Time to Market
Wistron is obligated and committed to ensuring the best time to market for its customers. The product management unit regularly reviews new product development and quality verification progress, while monitoring any unachieved quality goals in the plant during the pilot run and mass production. Wistron analyzes the cause of product defects based on four dimensions: people (personnel), machinery (equipment and tools), material (materials and components), and method (test and operational regulations). In addition, improvement and preventive measures based on analysis results are implemented to ensure the products are delivered on time.
Wistron endeavors to deliver zero-defects and competitive products and services to customers on time. Customer satisfaction is a key customer feedback indicator. We regularly collect information and suggestions regarding customer satisfaction or feedback on the needs of our customers from our quarterly business review (QBR) and use them as items for continuous improvements to pursue 100% customer satisfaction.

Wistron incorporates green product management practices in accordance with the ISO9001 Quality Management System and has obtained the IECQ QC 080000 management system certification. The raw materials of Wistron parts must abide by international or regional environmental regulations (e.g., RoHS, REACH, etc.), local government environmental policies (e.g, China RoHS, Japan RoHS, California Proposition 65, etc.), voluntary environmental regulations (China Compulsory Certificate (CCC), Electronic Product Environmental Assessment Tool (EPEAT), etc.), and special environmental regulations (e.g., conflict minerals, etc.) All of Wistron's product lines comply with EU RoHS regulations. As requested by our customers, we also avoid using specific hazardous substances that are harmful to the human body or the environment (e.g., halogen-free perfluorooctanesulfonic acid and polycyclic aromatic hydrocarbons).
Wistron develops products in compliance with customer requirements, local energy laws and regulations, and safety regulation labels from different regions, such as Energy Star. These labels are then affixed on product exteriors, packaging, or instruction manuals. Different product lines have passed energy consumption regulations of different regions, such as the European Union's ErP, South Korea's E-Standby, and China Energy Label, as requested by our customers. In 2019, more than 97.22% of mass production products such as laptops, desktop computers, and LCD monitors obtained the ENERGY STAR certification pursuant to the strategic requirements of energy demand.
Wistron's products protect consumer safety and health
Wistron Safety Laboratory has obtained the UL Client Test Data Program certification. This lab regularly reviews the laboratory quality plan through certification units to meet the ISO 17025 standard and periodically confirms the test data to maintain its testing capability and quality to protect consumers and their property. All Wistron mass production products are 100% compliant with IEC 60950-1 safety standards under the information technology equipment (ITE) category, and 100% compliant with IEC 60065 safety standards under the Audiovisual (AV) product category. With the advancement of technology, different types of products are being developed, making product classification extremely difficult. Wistron actively integrates the new standard IEC 62368-1 into its product design, becoming the first system manufacturer to pass the new standard and meet the test qualification in Asia. To prevent potential risks, Wistron shifts from passively abiding by safety requirements to actively preventing potential risks so as to ensure that all types of products completely meet safety regulations to further protect consumers' health and safety. Not only do all products become certified before they are sold in the market, product safety is consistently and continuously checked from time to time after mass production.
In 2019, all product lines were completely compliant with customers' requirements and local energy laws, and energy and safety labels, and was not involved in violations of voluntary regulations as well as laws and regulations concerning product information labeling.
A Focus on Product Liability and Product Quality Management
In today’s rapidly changing business environment, excellent product quality is a significant determinant of a company's operating status and the foundation of the company’s competitiveness. To guarantee high product quality, Wistron utilizes an ISO-based quality management system and implements a quality policy that states: 'To deliver defect-free, competitive products and services to our customers on time.' In accordance with this quality system and policy, Wistron adopts a top-down approach to monitor, measure, analyze, and continuously improve quality-related indicators; strictly implement related control process of “speaking, writing, and doing”; and manage daily operations with the plan-do-check-act (PDCA) practice so as to ensure that our quality goals are specifically implemented.
Wistron Laptops & Desktops Driver Downloads
Product quality verification
Wistron's product designs must pass relevant quality verification tests to ensure that products meets specifications and customers’ quality requirements before mass production, including functional verification, compatibility tests, reliability verification, environmental specification requirements, and the DFx (Design For Manufacture/ Assembly/ testing/ Service). Meanwhile, through the establishment of the Lessons Learned database and early participation in the product design and experimental stages of Wistron's factory, the product design capability, ease of production, and quality of produced products are continuously improved.
Supplier Quality Management
The quality of products produced is positively related to the quality of raw materials. Therefore, before production and use, Wistron will confirm that the raw materials meet the specifications and quality requirements, and will list the quality of raw materials as a key item for rating suppliers. Quality management auditing is also performed on suppliers. Wistron requests suppliers to improve non-conforming items in quality management or auditing by a specific deadline, and concurrently conducts quality control on materials and supply chains in order to ensure that the quality of the products produced adheres to customer requirements and specifications.
By organizing a green supplier conference, Wistron guides suppliers to strengthen their actions and response to the latest requirements of international environmental laws, improve their product quality, collectively build a green supply chain for Wistron, and work hand in hand to strive toward product sustainability and development. The 2019 Wistron Green Supplier Conference was held in Taipei, Zhongshan, Kunshan, and Chongqing, with over 900 participants. During the Green Supplier Conference, Wistron collaborates with technologists to share with suppliers Wistron's CSR practices and regulatory trend, introduce the Wistron supplier questionnaire survey platform (SQP), and teach suppliers practical operations through GPM system completing on the Material Composition Declaration (MCD) and Full Material Disclosure (FMD). In addition, RoHS testing method was used to educate all supplier partners on Wistron's strategic requirements and implementation methods with regards to “green environmental protection” to ultimately improve corporate quality management, promote the sustainable development of electronic industries, and fulfill corporate social responsibility.
Time to Market
Wistron is obligated and committed to ensuring the best time to market for its customers. The product management unit regularly reviews new product development and quality verification progress, while monitoring any unachieved quality goals in the plant during the pilot run and mass production. Wistron analyzes the cause of product defects based on four dimensions: people (personnel), machinery (equipment and tools), material (materials and components), and method (test and operational regulations). In addition, improvement and preventive measures based on analysis results are implemented to ensure the products are delivered on time.
Wistron endeavors to deliver zero-defects and competitive products and services to customers on time. Customer satisfaction is a key customer feedback indicator. We regularly collect information and suggestions regarding customer satisfaction or feedback on the needs of our customers from our quarterly business review (QBR) and use them as items for continuous improvements to pursue 100% customer satisfaction.
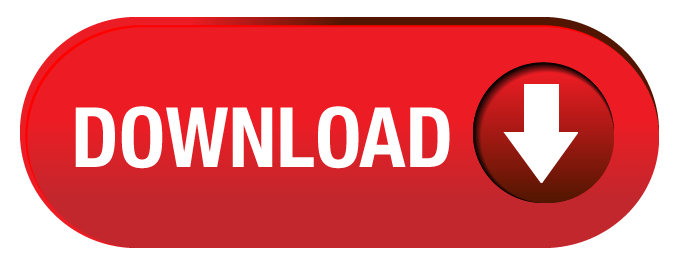